The main material for the production of panel furniture is
- Particle Board (PB)
- Medium Density Fiberboard (MDF)
- High Density Fiberboard (HDF).
Supporting materials include edging, honeycomb, PVC laminated, paper laminated, veneer, paint, glue, touch up, thinner and accessories such as dowels, elite, hinges, screws and rails.
Panel furniture products are made through several process stages including:
- Main material cutting process (Cutting)
- Forming process (Shaping)
- Drill process (Drilling)
- Edging process
- Lamination process
- Process of finishing and packing
The main material dimension standard is 1220mm x 2440mm applicable to all types of main materials PB, MDF and HDF. The main material thicknesses are 36mm, 25mm, 18mm, 15mm, 12mm and 9mm. Except for MDF and HDF materials, the thickness is even smaller, 4.7mm and 2.5mm.
The main material dimensions above are often used in the panel furniture industry. For different dimensions obtained through special orders to the manufacturer of this main material.
The cutting of the main material follows the cutting pattern according to the design according to the rules of efficiency so that the main material waste is reduced. This cut pattern applies a system of joining several cut patterns for each component of other furniture products.
The cut pattern design is made by PPIC so that the main material requirements for producing 1 order process can be estimated.
For example, a cupboard has several cupboard components as follows:
- Top component (Top Cover)
- Bottom Component (Bottom Cover)
- Side components (Side Cover)
- Middle component (Center)
- Components are fixed inside (Fixed Shelf)
- Components are installed not fixed inside (Adjustable Shelf)
- Drawer (Front Drawer)
The cut components are then arranged according to the type of component and pushed into the forming process. The arrangement of the components is neat and the number is even for each pallet of the arrangement and is accompanied by a process identity such as a kanban (introductory card for the production process).
2. The process of forming (Shaping)
Includes grooving and profiling processes. The grooving process is the process of making parallel lines of a certain size.
The function of grooving is to place the ends of other components so that they are clamped in the grooving.
The profiling process is the formation of certain radial sections on the outside of the component to form a certain radian size (R).
This shaping process can be done manually using a Router machine and Spindle machine and automatically using an automatic machine such as a double end machine.
Some components are a mixture of PB and MDF and these are called frame components. Inside the frame is filled with honeycomb material to strengthen the frame components which are covered with 4.7 mm MDF sheets on the top and bottom surfaces.
The process of this frame component uses glue so it needs to be pressed with a press machine for about 20 minutes before proceeding to the next formation.
3. Drill process (Drilling)
The process of making holes in components for dowel, elite or screw holes. The drilling process uses manual drilling machines, automatic drilling machines and CNC machines depending on the level of complexity of the drill pattern and the number of drills on each component.
The potential for rejection is very high in the drilling process such as wrong size of the drill hole, the wrong depth of the drill hole, the distance between the drill holes is different, the edges of the drill holes are uneven and the position of the drill holes is a few millimeters off the mark.
When a drill error occurs, it has the potential to replace all components in 1 production order. For example, 1 production order totaling 500 sets will result in waste of 500 components of the wrong drill.
Tips on preventing drill errors can be done by checking the drill results for every 30 components that are processed. In addition, for drilled components, assembly must be carried out with other types of components so that it can be seen whether the construction is appropriate or not.
4. Process of edging
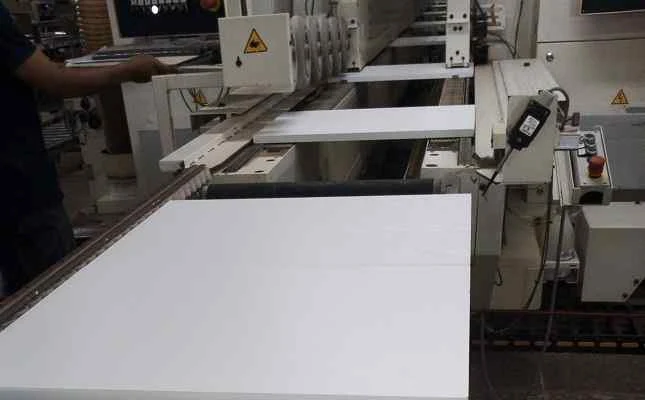
Coating the edge surface of the component using PVC or paper edging material. The number of sides of the surface that is coated depends on the construction of the furniture, it can be only 1 side or all the sides of the surface. Standard components have 4 straight surfaces.
What if one or more of the surfaces are curved or wave-shaped?
The shape of the non-straight side surface cannot be processed using an automatic edging machine but must be done by a manual edging machine.
The edging results between automatic edging machines and manual edging machines are the same in quality but the cycle time is different because the process in the manual edging machine is edging by the operator one by one and there is no machine speed setting.
5. Lamination process
Is the process of coating the upper and lower surfaces of components using PVC, paper or veneer laminated materials so that they appear colored like the natural color of wood or a specified color. Examples of natural wood colors include cyclone oak, brown oak, acacia, cyclone walnut and euro oak.
For the main material to be formed, straight components and flat component surfaces, the lamination process can be carried out before the main material is cut, namely using a lamination machine for standard material sizes.
This can save the process time base because it eliminates the lamination process per component which can reach thousands of pieces.
However, the type of soft component in the form of a radial side surface means that the initial lamination process cannot be carried out.
6. Finishing and packing process
Components resulting from the lamination process have residual glue attached to the edges/finish edges of the glued surface and this must be cleaned until there are no traces of the glue. How to clean using a white cotton cloth moistened with thinner.
After cleaning the remaining glue, it is necessary to ascertain whether there is a gap between the edging edge and the top and bottom surface edge which may be caused by reject edging such as over trimming, bubble edging, scoring and chipping. If there is a gap, cover it immediately using paint that is the same color as the color of the lamination (touch up).
Laminated components and other non-laminated components are then prepared in the packing area for immediate packing according to the item's "packing arrangement" guideline.
Flea Beetles Cause Damage to Furniture
The flea beetle from a new species of the wood-eating beetle family is a type of wood-eating insect, both solid wood and processed wood and causes cavities in the wood so that the flea beetle is a big problem faced in the furniture industry because it causes damage to the main material to the finished product if eaten by these flea beetles so that there is a need for a complete solution to it.
Characteristics of flea beetles:
- Dark black in color
- Up to 6mm long
- Rectangle texture, 2/3 body and 1/3 head
- Make a hole in the wood
- Can run fast like an ant and can fly.
We focus on flea beetles and how to deal with them.
Quick action is needed to overcome the disturbance of flea beetles so that plant operations continue and their handling is complete so as to avoid losses in the future.
The quick way to completely deal with flea beetles and has been proven successful until not a single flea beetle is found based on real experience in the furniture industry:
- Identify the causative source of flea beetles
- Fumigation
- Material protection
- Participation of all employees
Make sure that the flea beetle has been identified as the source of its spread.
There are 2 potential sources of infestation of flea beetles
- From material suppliers
- Conducive environment
If no flea beetles are found, then the wood material is safe.
Pay attention to the conducive environment for the spread of flea beetles. Flea beetles can be carried by non-material wood materials.
For example, in one of the furniture industries in Tangerang, with a large factory environment, there are many geese kept in the back area of the factory. Flea beetles can be carried into the plant and hide in goose foods such as bran.
Therefore, you should not keep poultry in the furniture factory environment.
2. Fumigation
It is impossible to catch individual flea beetles by human hands because there are thousands of flea beetles. Most can catch just a few tails even though the development of flea beetles is very fast.
Fumigation is a method of eradicating pests by fogging using pesticides or insecticides.
Fumigation is the most effective method compared to other methods such as injecting wood insecticides and coating wood using insecticides.
Fumigation is proven to overcome the plague of mosquitoes, rats and cockroaches. But this fogging method can be used to quickly and precisely deal with flea beetle outbreaks.
Choose a trusted fumigation or pest control service provider. Convey that the purpose of fumigation is to overcome flea beetles so that the insecticidal liquid ingredients are suitable for fogging purposes. Ask for a guarantee that the fumigation results are effective and no flea beetles are found later.
Implementation of fogging outside working hours or on Saturday or Sunday holidays. Fogging that is done during working hours will interfere with employee work activities so it is not recommended to do it during working hours.
Fogging target:
- Particle board material, flea beetles really like sawdust in a solid, hard and not moist form.
- MDF and HDF materials, especially those that have holes from the drilling machine process, flea beetles find it difficult to eat MDF and HDF materials but can breed or hide in these material holes.
- Solid material, the same as particle board, is very popular with flea beetles.
- The 20 meter radius area includes culverts and gutters because flea beetles can fly away from the fogging smoke.
3. Material Protection
About 1 hour after fogging, all wood material is protected by wrapping it with stretch film. Flea beetles are unable to penetrate this stretch film layer so that the material is protected.
The stretch film is transparent so that it can be seen whether the wood material still has live beetles because when wrapped in the stretch film the beetles are actually already inside the material.
The stretch film can be removed when the wood component is processed and wrapped again with the stretch film when it becomes WIP.
4. Participation of All Employees
When fogging and protecting wood materials have been carried out, all employees participate in checking for the presence of beetles while carrying out their work activities.
This is anticipated if the results of fogging are not complete, leaving flea beetles hiding. Immediately report to the PIC, usually the GA, for re-fogging for new findings of flea beetles.
Loading posts